Impact Gloves vs. Cut-Resistant Gloves: What's the Difference
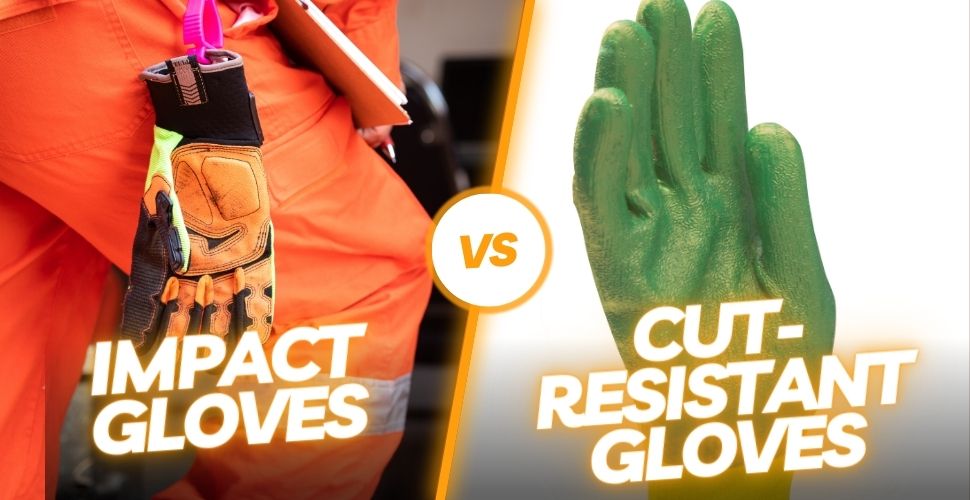
Your hands are your most valuable tools in the construction industry. That's why choosing suitable gloves is crucial for protection and productivity. But when faced with sharp materials or heavy impacts, how do you decide between cut-resistant and impact gloves? Let's dive into the key differences that will ensure you make the best choice for your safety.
Impact Gloves vs. Cut-Resistant Gloves: 10 Key Differences
Impact Gloves and Cut-Resistant Gloves serve different purposes in protecting workers from various workplace hazards. Let's understand ten key differences.
1. Purpose:
Workers need protection from all sorts of hazards. Cut-resistant gloves are your shield against sharp edges. They use rigid materials like Kevlar, Dyneema, or even stainless-steel mesh to provide an exceptional barrier against knives, blades, and other cutting tools.
On the flip side, impact gloves take the blows. They feature padding on the palms, knuckles, and the back of your hand to absorb and spread out the force of heavy hits, crushing injuries, or dangerous pinches. It protects from falling objects, tool strikes, and powerful machinery.
Key Takeaway: Cut-resistant gloves protect against cuts; impact gloves protect against blunt force. Knowing the risks on your job site is the first step to choosing the proper protection.
2. Protection:
Cut-resistant gloves are your defence against sharp edges and tools. Materials like Kevlar or specialised fibres create a powerful barrier, minimising the risk of cuts, gashes, and scrapes. These gloves are a must-have if your job involves blades, glass, or other dangerously sharp materials.
Impact gloves are designed to take a hit. These gloves often feature thermoplastic rubber (TPR) padding to absorb and spread the force of heavy blows. Suppose falling objects, powerful tools, or machinery are part of your daily work. In that case, impact gloves help protect your hands from painful injuries like bruises, fractures, or crushing.
Key Takeaway: Cut-resistant gloves protect against slices and cuts. Impact gloves shield against blunt force injuries.
3. Materials:
Cut-resistant gloves rely on super-strong materials like Kevlar. This incredible fibre protects against blades, tools, and other sharp hazards.
Impact gloves need a different kind of toughness. Thermoplastic rubber (TPR) gives them shock-absorbing power. This flexible material disperses the force of sudden impacts, protecting your hands from the blow.
Key Takeaway: The materials used in each type of glove directly serve their unique protective purposes.
4. Resistance Levels:
Cut-resistant gloves have specific ratings that tell you how much protection they provide. These ratings help you choose the right glove for your risk level. Consider them a safety guide for your hands!
Impact gloves also offer varying degrees of protection. Look for features like reinforced padding on the back of the hand and fingers. The more padding, the more protection you'll have against crushing blows and impacts.
Key Takeaway: Different types of gloves offer different types of protection. Understanding the specific risks you face is crucial for choosing the right ones.
5. Hazards Addressed:
Cut-resistant gloves are your best defence against sharp objects. Handling materials like glass and metal or working with knives and tools calls for the specialised protection they provide.
Impact gloves are essential when crush injuries are a risk. Think heavy machinery, falling materials, or powerful tools that can cause impact injuries. These gloves protect your hands from painful, or even life-changing, damage.
Key Takeaway: Know the specific hazards of your job and choose the safety gloves that match those risks.
6. Work Environments:
Cut-resistant gloves are a must-have if you're working with anything sharp. Contractors handling saw blades, glass, and utility knives rely on these gloves to keep their hands safe. Mechanics working with sharp vehicle parts and broken glass also need the protection they provide.
Impact gloves are essential on job sites where there's a risk of hands getting crushed or pinched. Manufacturing plants with heavy machinery, construction sites with moving equipment, and even oil and gas workers handling heavy tools – these jobs demand impact protection.
Key Takeaway: When choosing gloves, think about the specific dangers your workers face on the job each day.
7. Regulations:
Employers, it's your responsibility to determine what risks are at your worksite. It includes heat, cuts, punctures, and crushing injuries. The Occupational Safety and Health Association (OSHA UAE) sets workplace safety standards.
Choosing the suitable gloves for the job is part of meeting these requirements. Different hazards demand different gloves. Just like you need heat-resistant gloves for high-temperature work, you need cut-resistant gloves for handling sharp materials.
By providing the proper protective gloves, you're not just following the law but creating a safer workplace. These gloves can protect against injuries, prevent accidents, and help your workers feel secure.
Key Takeaway: Choosing the right gloves for the job is crucial, but remember training. Correct use and regular inspections are just as important for safety.
8. Injuries Prevention:
Cut-resistant gloves save hands from serious harm. Their specialised materials, like Kevlar, stand firm against sharp blades, broken glass, or dangerous tools. For workers handling these hazards, the protection they offer is critical.
Impact gloves help prevent the painful, life-altering injuries that heavy jobs bring. These gloves are specially designed to disperse the force of blows. They act as a shield, protecting against broken bones, crushed fingers, or worse, when accidents happen.
Key Takeaway: Both gloves prevent workplace injuries, but each tackles different risks.
9. Design Features:
Impact gloves are all about cushioning. Padding on the palms protects against the constant vibration of power tools. This vibration protection can help prevent chronic problems like Hand-Arm Vibration Syndrome (HAVS). The backs of impact gloves often feature thermoplastic rubber (TPR), which adds extra protection from falling objects or machinery accidents.
Cut-resistant gloves rely on super-strong materials. You'll find fabrics like Kevlar or even stainless steel in many designs. These gloves fit snugly to give you the best possible coverage. They may also have unique textures or coatings to enhance your grip on slippery or sharp materials.
Key Takeaway: The design of each type of glove directly matches the dangers they're made to protect against.
10. Standardisation:
Official standards exist to ensure impact gloves protect your hands. These standards set minimum levels for resisting impact forces on knuckles and fingers. Look for a rating of 1, 2, or 3 – higher, which means more excellent protection for jobs with crushing severe risks.
Cut-resistant gloves also have strict standards. These tests measure how well gloves withstand cuts and prevent injuries. Kevlar and similar materials are used because they score high on these tests.
Key Takeaway: When buying any safety glove, look for standard ratings. These guarantee the gloves have been tested and proven effective.
Impact Gloves vs. Cut-Resistant Gloves: Comparison Table
Feature |
Impact Gloves | Cut-Resistant Gloves |
Purpose | Protect against impact injuries, crushing blows, and pinch points. |
Protect against cuts, lacerations, and abrasions from sharp objects. |
Protection | Absorb and disperse impact energy to reduce the force transmitted to the hands. |
Provide a barrier against sharp edges and objects, preventing cuts and punctures. |
Materials | Often incorporate thermoplastic rubber (TPR), padding, and reinforced materials in the back of the hand and fingers. |
Frequently made with Kevlar, Dyneema, stainless steel mesh, or other high-performance fibres. |
Resistance Levels |
Rated on their ability to absorb impact, with higher levels offering more protection. |
Tested and assigned cut-resistance ratings based on materials used and protection against sharp hazards. |
Hazards Addressed |
Impacts from tools, falling objects, heavy machinery, crushes, and pinch-point injuries. |
Cuts and abrasions from knives, blades, glass, sharp metal, and other cutting hazards. |
Work Environments |
Construction, manufacturing, oil and gas, mining, and other heavy industries with impact risks. |
Construction, automotive, manufacturing, food processing, glass handling, and any industry with sharp materials. |
Regulations |
Fall under general OSHA hand protection requirements. Standards exist for impact rating levels. |
Comply with OSHA regulations. Standards are in place for cut-resistance ratings, ensuring effectiveness. |
Injuries Prevention |
Reduce fractures, bruises, amputations, and crush injuries. |
Minimise cuts, lacerations, and puncture wounds. |
Design Features |
Padding on palms and knuckles, back-of-hand reinforcement, vibration reduction elements. |
Close-fitting design, specialised high-strength materials, enhanced abrasion resistance, and textured coatings for grip (optional). |
Standardisation |
Impact performance levels (1-3) established by standards bodies. |
Cut-resistance ratings are assigned based on testing and performance. |
Final Words
Understanding the difference between cut-resistant and impact gloves empowers you to make the right choices for your workers. By matching the specific risks of the job to the correct type of gloves, you're not just protecting hands; you're investing in a safer, more confident workplace.